Denver Children’s Hospital — Aurora, CO
White Maple Veneer with Clear Finish
SKU(s):5216-12, 4400-Custom
Featured Systems
5200 Staggered Perf Tile
Staggered perforations create a vibrant appearance and exceptional acoustic performance.
4400 Torsion Spring Tile
This full-access panel uses HD 15/16” T-Bar. Hardware keeps reveals true, stiffeners keep panels flat.
Featured Article
What are the Types of Suspended Acoustic Ceilings?
A suspended acoustic ceiling is a secondary ceiling, hung below the structural ceiling both to treat room acoustics and to look attractive.Featured Video
Wood Tiles – The Most Common Questions [VIDEO]
Introduction Michael Roemen: “Hey everybody, we’re excited for you joining us in today’s video. Kat and Derek will be talking about wood ceiling Tiles…Project Details
Healthcare
ZGF Architects, Portland, Oregon
Acoustical Services, Denver, Colorado
38,000
November 2006
2007 CISCA Award of Excellence (Gold, West Region, Ceilings)
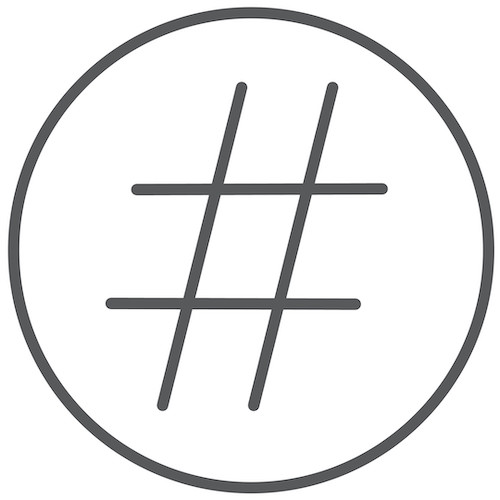
0191